Выход человечества в космос стал возможен не только благодаря инженерной мысли в ракетостроении, но и благодаря фундаменту, который задолго до этого заложили металлурги. Без сверхпрочных, жаростойких и коррозионностойких сплавов не взлетел бы реактивный самолёт, не вышел бы на орбиту спутник, не заработал бы ядерный реактор.
Сегодня мы поговорим о суперсплавах — материалах, на которых построена современная высокотехнологичная инженерия. Суперсплавы — это группа металлических материалов, способных работать там, где обычные металлы выходят из строя. При температурах от 600 до 1100 °C они сохраняют прочность, не деформируются под нагрузкой, сопротивляются окислению и выдерживают циклические перегрузки.
Термин superalloy (суперсплав) появился в США в середине 1940-х годов, так называли сплавы, созданные для авиационных турбин и турбокомпрессоров. В СССР аналогичные материалы называли жаропрочными сплавами. Их развитие было тесно связано с реактивной авиацией, ракетными двигателями, ядерной и газотурбинной энергетикой.
Основные свойства суперсплавов:
• Жаропрочность — сохраняют несущую способность при высоких температурах длительное время.
• Устойчивость к ползучести — не деформируются под длительным воздействием давления и тепла.
• Коррозионная и окислительная стойкость — выдерживают агрессивные газовые среды.
• Стабильность структуры — сохраняют внутреннюю структуру при многократных перегрузках.
Эти материалы незаменимы там, где одновременно действуют высокая температура, давление, агрессивная химическая среда, и предъявляются критические требования к надёжности.
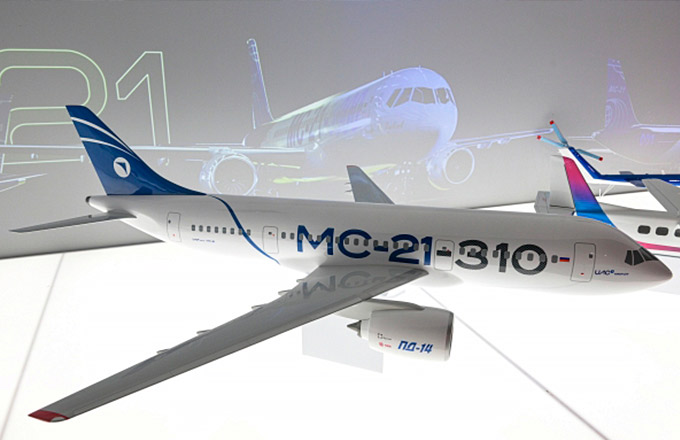
Без суперсплавов невозможно себе представить, например, развитие современной авиации.
Когда сталь перестала справляться
На рубеже XIX и XX веков электротехника переживала стремительный рост — новая, почти футуристическая отрасль, сопоставимая по масштабам прорыва с космической техникой середины XX века.
Лампочки зажигались нажатием кнопки, по улицам вовсю курсировали электрические трамваи, в промышленных цехах электродвигатели постепенно вытесняли паровые машины, открывая новую эру промышленной эффективности.
Но довольно быстро стало ясно: традиционные материалы, пригодные для паровых систем, не выдерживают тепловых и электрических нагрузок новой техники. Высокие температуры, токи, вибрации — всё это разрушало проводку, контакты и металлические элементы.
Перед инженерами встала новая задача: создать металл, который не плавится, не окисляется и не теряет форму при длительной работе в условиях высокой температуры и длительного окисления. (При температурах выше 500 °C любой металл начинает взаимодействовать с кислородом воздуха.)
Одним из первых ответов на этот вызов стал нихром — никель-хромовый сплав, изобретённый в 1905 году американским инженером Альбертом Маршем. Нихром сочетал высокую термостойкость с химической стабильностью в воздухе, что сделало его идеальным материалом для нагревательных элементов: электропечей, промышленных резисторов и сушильных установок.
Хотя нихром и не был суперсплавом в полном смысле этого термина — он не работал под механическими нагрузками, — именно он впервые продемонстрировал, что сплав никеля и хрома может сохранять стойкость к высоким температурам и окислению.
Эта идея стала основой для дальнейших разработок: никель сохранили как базовый металл, а для повышения жаропрочности начали добавлять кобальт и другие элементы.
Систематические исследования жаропрочных сплавов начались в конце 1930-х годов на фоне стремительного развития авиации и появления газотурбинных двигателей. В этот период разрабатывались как никелевые суперсплавы, легированные кобальтом и другими элементами, так и отдельные кобальтовые суперсплавы.
Однако именно никель стал основой для большинства авиационных и энергетических решений. Так в 1930–40-х годах появились первые «настоящие» суперсплавы — жаропрочные материалы, способные выдерживать экстремальные температуры и механические нагрузки. Они стали фундаментом новой высокотемпературной металлургии и заложили базу для технологических прорывов в авиации и энергетике.
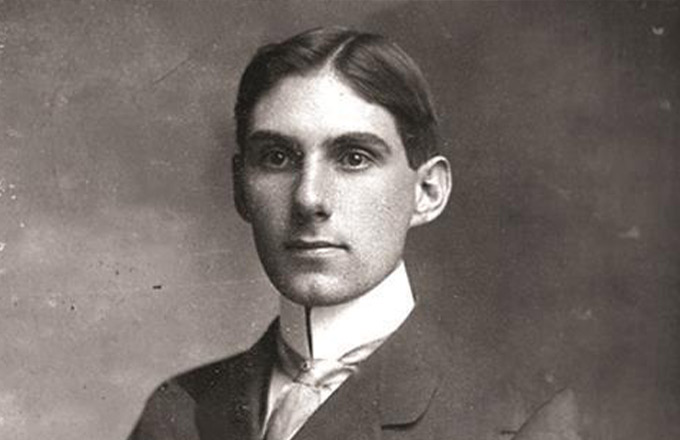
Американский инженер Альберт Марш, который изобрёл нихром.
Суперсплавы — металл высоких скоростей
Авиация стала первым и главным полигоном для внедрения суперсплавов. С ростом нагрузок, температур и скоростей в 1930–40-х годах возникла острая потребность в жаропрочных материалах — особенно для турбонагнетателей и газотурбинных двигателей.
Сталь выдерживала первые нагрузки, но быстро подошла к своему пределу: при 500–600 °C её прочность стремительно падала, тогда как новые газотурбинные двигатели требовали работы при 800–1000 °C. Кроме того, чтобы выдерживать такие нагрузки, стальные детали приходилось делать массивнее, что противоречило самому духу авиации.
Так началась история суперсплавов — материалов, способных работать там, где сталь уже не справлялась.
В Великобритании компания Henry Wiggin & Co разработала серию никелевых сплавов — Nimonic — специально для проекта первого турбореактивного двигателя, созданного Фрэнком Уиттлом, одним из пионеров реактивной авиации.
Параллельно активные работы шли и в США, где появился сплав Inconel. В Германии также разрабатывали жаростойкие никелевые материалы для авиации, особенно в рамках создания реактивных двигателей.
После Второй мировой войны термин «суперсплав» стал широко использоваться для описания сплавов, предназначенных для работы в турбонагнетателях и авиационных турбинах, требующих высокой производительности при повышенных температурах.
Со временем область применения суперсплавов расширилась: они нашли своё место в газовых турбинах для электростанций, ракетных двигателях и оборудовании для химической и нефтяной промышленности.
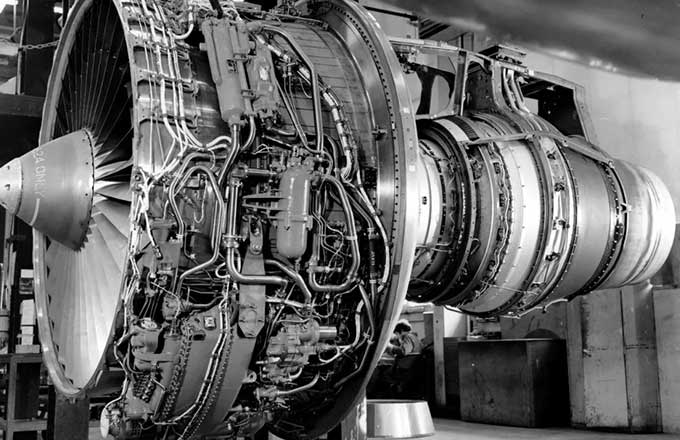
Суперсплавы нашли своё место в газовых турбинах для электростанций.
Вклад советских металлургов
СССР включился в гонку за создание суперсплавов чуть позже, но уже в 1950-е годы сформировал собственную научную школу жаропрочных никелевых сплавов, которая быстро заняла важное место в авиационной металлургии.
Ключевую роль сыграли ведущие научно-исследовательские институты — ВИАМ и ВИЛС, где создавались материалы, способные выдерживать экстремальные температуры и нагрузки.
Суперсплавы применялись в авиационных и ракетных двигателях — прежде всего в турбинах, камерах сгорания и других нагруженных узлах. Эти разработки обеспечили СССР технологическую независимость и позволили активно конкурировать с западными странами в ключевых сферах — от военной авиации до космической техники.
Отличия советской и западной школ суперсплавов
Хотя задачи перед конструкторами были схожими — создание материалов, способных работать при экстремальных температурах и нагрузках, подходы в СССР и на Западе существенно различались. На Западе ставка делалась на максимальную эффективность, ресурс и термостойкость.
Для этого широко использовали дорогие легирующие элементы (например, рений и тантал) и сложные литейные технологии, включая направленную кристаллизацию и монокристаллическое литьё. (В СССР переход к этим технологиям начался только в 1980-х годах.) Такие материалы были идеальны для турбин, рассчитанных на длительную и экономичную работу как в авиации, так и в энергетике.
Советский подход был иным: в условиях ограниченных ресурсов и ориентации на массовое производство предпочтение отдавали сплавам с более доступными компонентами и высокой технологичностью.
Двигатели проектировались так, чтобы выдерживать экстремальные перегрузки и при этом оставаться ремонтопригодными. Надёжность в боевых условиях и простота серийного производства зачастую ставились выше абсолютного ресурса.
Эти различия отражались не только в химическом составе материалов, но и в самой философии инженерного проектирования: западная школа стремилась к длительному ресурсу, советская — к максимальной живучести.
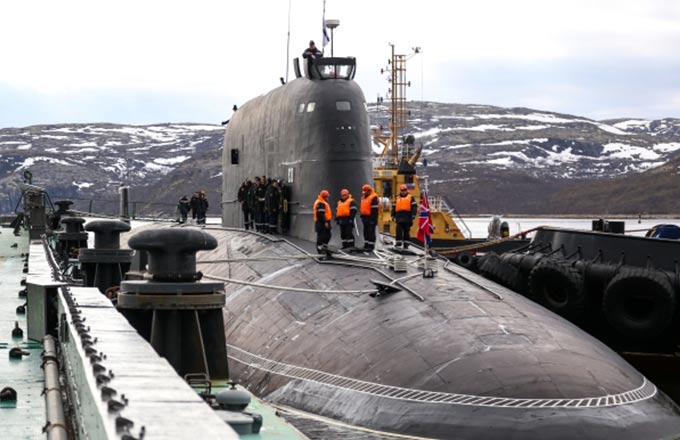
Отечественные подводные лодки тоже делают из суперсплавов.
Суперсплавы в ключевых отраслях техники
Развитие металлургии высокотемпературных сплавов открыло новые возможности для авиации, космоса, флота и энергетики. В каждой из этих сфер экстремальные условия эксплуатации диктовали свои особые требования к материалам — и именно суперсплавы стали ответом на эти вызовы.
Авиация
В авиационных газотурбинных двигателях суперсплавы выдерживают температуры свыше 1000 °C и многократные циклические перегрузки. Из них изготавливают турбинные лопатки, диски роторов и другие критически важные детали.
Ракетная техника
В ракетных двигателях суперсплавы работают в условиях экстремального нагрева и агрессивных газовых сред. Они применяются в камерах сгорания, соплах и форсунках, сохраняя прочность и устойчивость к окислению при запредельных нагрузках.
Флот
На кораблях, подводных лодках и атомных ледоколах суперсплавы и коррозионностойкие никелевые сплавы применяются в наиболее нагруженных элементах энергетических систем — турбинных лопатках, насосах, теплообменниках.
Материалы должны сохранять прочность при высоких температурах, устойчивость к коррозии в морской воде и надёжность в условиях высоких механических нагрузок.
В системах атомных подводных лодок применяются также суперсплавы на основе кобальта — в узлах, где требуется сочетание жаропрочности, коррозионной стойкости и устойчивости к радиационному облучению в экстремальных условиях.
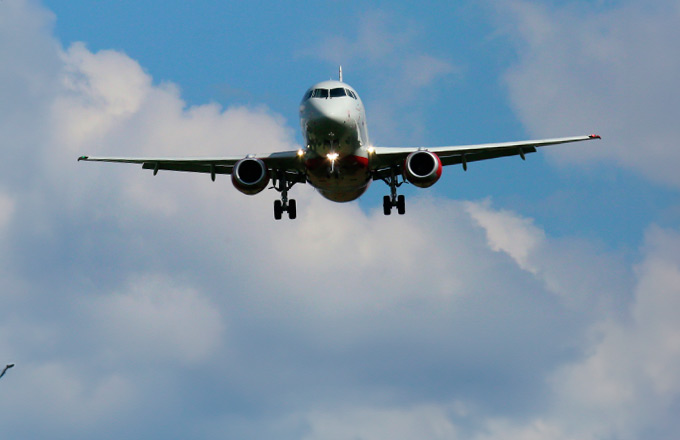
В авиационных газотурбинных двигателях суперсплавы выдерживают температуры свыше 1000 °C.
Ядерная энергетика
В ядерных реакторах суперсплавы работают в условиях высоких температур, нейтронного облучения и агрессивных теплоносителей. Они используются для изготовления элементов теплообменников, трубопроводов и оболочек топливных сборок, обеспечивая надёжность и безопасность работы реакторов.
Никелевые и кобальтовые суперсплавы стали основой для создания высоконагруженных конструкций в авиации, ракетной технике, на флоте и в энергетике. Их способность сохранять прочность, стойкость и надёжность в экстремальных условиях определила технологический прогресс в ключевых отраслях современной промышленности.
Итак, суперсплавы стали неотъемлемой частью развития авиации, космоса, флота и энергетики. Каждая сфера предъявила к ним свои особые требования:
• Авиация: высокие температуры, циклические перегрузки.
• Ракетная техника: экстремальные температуры, агрессивные газы.
• Флот (надводные корабли): коррозия в морской воде, усталостная прочность.
• Подводный и атомный флот: радиационная стойкость, коррозия, высокое давление.
• Ядерная энергетика: высокие температуры, нейтронное облучение, агрессивные среды.
Суперсплавы решили задачи своего времени, но технологии требовали большего. И металлурги пошли дальше, открывая новые горизонты прочности и надёжности.
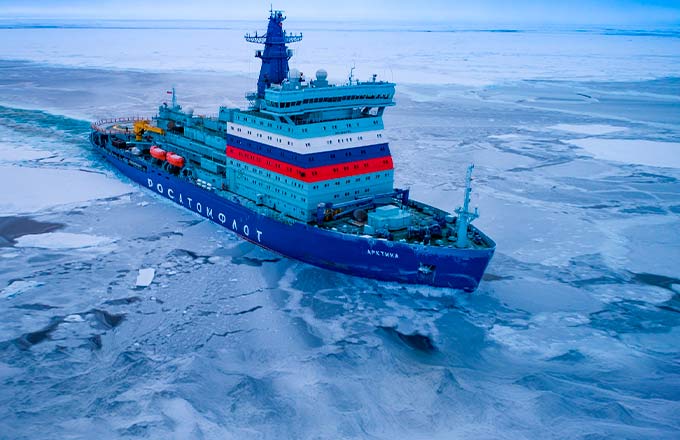
На атомных ледоколах суперсплавы применяются в наиболее нагруженных элементах энергетических систем — турбинных лопатках, насосах, теплообменниках.
Суперсплавы: путь к новой архитектуре материалов
Мы проследили путь суперсплавов от первых жаростойких материалов до сложных решений, применявшихся в ракетной технике, на флоте и в ядерной энергетике к 1980-м годам.
Мы увидели, как инженерная мысль искала баланс между температурой, прочностью и надёжностью — и как именно эти задачи определили облик целых отраслей.
Но самое интересное ещё впереди.
До 1980-х годов развитие суперсплавов шло медленно и требовало огромных усилий — от первых экспериментов к большим прорывам.
Однако с конца XX века развитие резко ускорилось: новые требования авиации, энергетики и космоса потребовали от материалов совершенно иного уровня свойств.
Всего за несколько десятилетий появились новые поколения суперсплавов, изменившие саму архитектуру материалов.
В следующей части мы расскажем о современном и перспективном развитии суперсплавов: о переходе ко 2-му, 3-му, 4-му и 5-му поколениям, о появлении градиентных структур и аддитивных технологий, включая 3D-печать жаропрочных металлов, о новом этапе кобальтовых суперсплавов и революционной концепции высокоэнтропийных сплавов — материалов, проектируемых как сложные системы с заданными свойствами.
Если в XX веке суперсплавы стали тем фундаментом, на котором строилась авиация и «космос», то в XXI веке они открывают путь к новой архитектуре материалов.
Вадим Чепига