Металлургическая отрасль переживает очередную цифровую революцию, в которой искусственный интеллект побеждает. ИИ занимает центральное место в процессах оптимизации производства, контроля качества и логистики. Используя ИИ, металлурги уменьшают свои издержки, повышают точность изготовления металлопроката и даже снижают уровень травматизма на производстве.
И всё же самый главный прорыв — ИИ научился прогнозировать качество металла. Специально обученные нейронные сети анализируют химический состав шихты, параметры плавки и прокатки, что позволяет с высокой точностью предсказывать механические свойства готовой продукции.
Что говорит об ИИ новый папа римский?
Папа римский Лев XIV провёл в субботу первую встречу с кардиналами после своего избрания главой католической церкви, назвав искусственный интеллект (ИИ) одной из важнейших проблем. Он глубоко убеждён, что ИИ создаёт проблемы для защиты «человеческого достоинства, справедливости и труда».
Расскажем о последних достижениях и планах внедрения ИИ на двух крупнейших отечественных предприятиях чёрной металлургии — ММК и «Северстали».
Где применяют ИИ в «Северстали»
Использование ИИ в промышленности — это следующий этап после автоматизации. С помощью алгоритмов машинного обучения можно найти скрытые резервы, в разы улучшить производственные показатели, менять технологию производства, влиять на качество выпускаемой продукции. Однако без базы в виде автоматизации невозможно получать качественные данные для дальнейшего обучения моделей.
«Северсталь» использует ИИ для повышения эффективности производства (увеличение производительности агрегатов, сокращение издержек, контроль работы оборудования), повышения качества готовой продукции, контроля за соблюдением техники безопасности, снижения экологической нагрузки. Кроме того, идёт внедрение ИИ в продажах и корпоративных процессах. Всего портфель проектов на данный момент насчитывает свыше 60 решений. Использование технологии ИИ уже приносит значительную рентабельность — в 2024 г. экономический эффект от проектов в этой сфере составил свыше 1 млрд рублей.
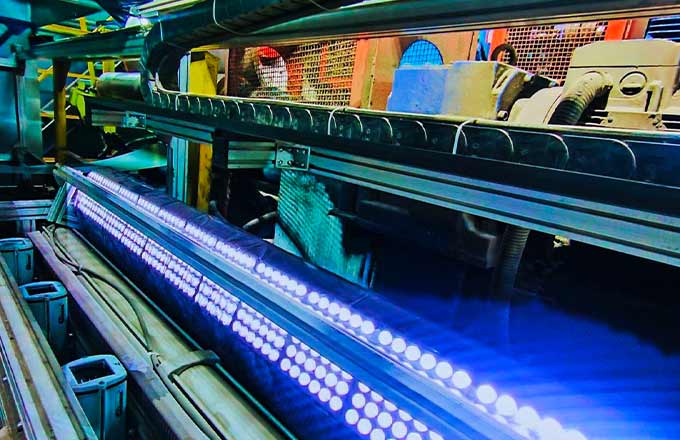
«Северсталь» масштабирует системы компьютерного зрения
Например, на самом большом стане горячей прокатки в России — стане 2000 ЧерМК — среднюю паузу при прокатке удалось снизить на 1 секунду на сляб, а эффект превысил 180 млн рублей. Внедрение экспертной системы доменного процесса, которая помогает с расчётом и подбором оптимальных технологических параметров подготовки и производства железорудного сырья, «принесло» 97,6 млн рублей.
Кроме того, платформа для видеоинспекции «Стальной взгляд» помогает фиксировать отклонения в технологических процессах, отслеживает состояние оборудования и контролирует безопасное нахождение персонала на рабочем месте. В частности, 12 систем на основе компьютерного зрения контролируют качество готовой продукции, распознавая отклонения по нескольким классам дефектов. На Яковлевском ГОКе внедрены модели, которые следят за безопасным выполнением работ с грузоподъёмными механизмами и в опасных зонах железнодорожного состава.
ИИ-модель управления агрегатом непрерывного горячего цинкования позволяет автоматически управлять нанесением покрытия, контролировать мощность печи и скорость линий с учётом технологических ограничений. Это решение позволило снизить расходы цинка на 1,5% и повысить производительность агрегата на 3,4%.
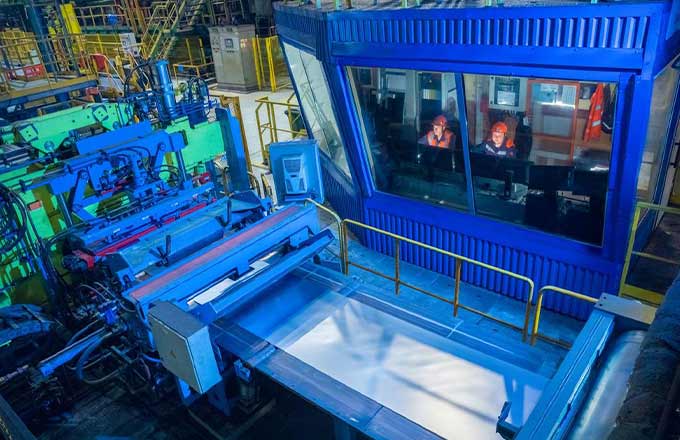
Агрегат непрерывного горячего цинкования предназначен для термохимической обработки стальной полосы для защиты от коррозии
Ещё одна ИИ-система для контроля производства окатышей позволяет автоматически управлять агрегатом и устанавливать оптимальные режимы работы очереди окомкования окатышей, что привело к повышению производительность линии на 11%. «В этом году мы планируем продолжить развивать проекты, направленные на повышение производительности агрегатов и производительности труда, разработку решений в области промышленной безопасности и цифровой аттестации продукции», — рассказали о своих планах «Про Металлу» в пресс-службе «Северстали».
Где применяют ИИ на ММК
В ММК теперь есть собственный Центр компетенций искусственного интеллекта, который разрабатывает высокотехнологичные решения. Его работа базируется на широком спектре технологий: прогнозирование (машинное обучение и статистическое моделирование), оптимизация, компьютерное зрение, большие языковые модели и многое другое.
Вообще, экономический эффект от внедрения ИИ-решений на Магнитогорском металлургический комбинате превысил 4,5 млрд рублей за 5 лет.
В марте 2025 года на ММК внедрили систему «умного» учёта выпускаемых труб. Система позволяет избежать ошибок при отгрузке труб. «В основе технического решения лежит технология из области искусственного интеллекта, интегрированная в специально разработанное веб-приложение. Для работы с ним работники листопрокатного цеха №8 используют планшеты, с помощью которых они фотографируют готовую продукцию. Система способна распознавать трубы различного диаметра и осуществить их подсчёт с точностью до 99,6%», — рассказали в пресс-службе комбината.
Полученная информация передаётся в базы данных предприятия для формирования отгрузочных документов. Уже на складе с помощью приложения персонал сканирует ярлыки на пачках труб для повторной проверки перед отправкой потребителю. «Раньше работники цеха и склада вручную считали трубы, количество которых может достигать в пачках почти 600 штук. Это приводило к несостыковкам и отправке потребителю недостающего или излишнего количества продукции. Новое решение полностью автоматизирует процесс и исключает возможность ошибок учёта», — отметил старший мастер ЛПЦ–8 Руслан Халапов.
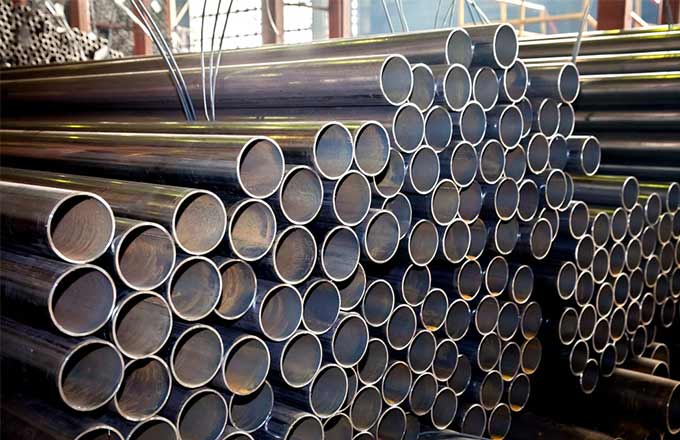
В марте 2025 года на ММК внедрили систему «умного» учёта оцинкованных труб
Один из самых масштабных проектов — цифровой помощник прогнозирования температуры заказа в электросталеплавильном цехе, разработанный с применением методов машинного обучения. До недавних пор специалист, управляющий доменным процессом, опирался в принятии решений исключительно на показания дискретных данных. Однако их значения могут быть некорректными в меняющихся условиях, что может привести к ошибочным рекомендациям системы-советчика. Теперь рекомендуемые параметры газодинамики выдаёт искусственный интеллект, обученный на исторических данных.
С начала года на комбинате работает автоматизированная система проверки характеристик листового проката на базе технологии машинного зрения. Высокотехнологичное решение оптимизирует производственный процесс и повышает качество продукции.
Технология работает следующим образом. На участке листоотделки толстолистового стана происходит сканирование движущегося проката, результаты поступают на сервер со специализированным программным обеспечением. Система анализирует изображение с камер машинного зрения и проводит автоматическую проверку геометрии листа, распознаёт, классифицирует и составляет 3D-карту дефектов поверхности проката. Одновременно выявляются соответствия или несоответствия заданным параметрам качества продукции для конкретного потребителя.
«Внедрив новое цифровое решение, мы снизили человеческий фактор при контроле качества продукции. Производительность линии резки может достигать до 80 листов в час, поэтому не исключена ошибка специалиста в измерении геометрии и идентификации дефектов поверхности. Система на базе технологии машинного зрения делает это быстрее и точнее», — отмечает руководитель проекта, заместитель начальника производства толстого листа по качеству Владимир Молгачёв.
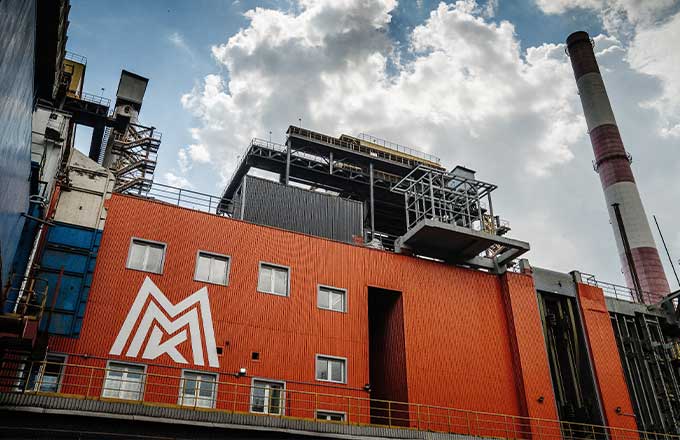
ММК активно использует ИИ для обработки больших объемов данных, оптимизации производственных процессов
По его словам, система значительно снижает риски получения несоответствующей нужным стандартам продукции и брака, позволяет исключить претензии клиентов по дефектам геометрии и поверхности листа.
На ММК искусственный интеллект следит в том числе и за безопасностью и здоровьем металлургов. В основе системы лежит программная платформа «Цифровой рабочий», интегрирующая в режиме реального времени данные локального позиционирования с носимых устройств, информацию о технологическом процессе, видеонаблюдение и видеоаналитику. С помощью технологии машинного зрения система обрабатывает информацию с сотен источников, отображая её в 3D-модели цеха. Анализ полученных данных не только предотвращает нахождение сотрудников в опасных зонах, но и выявляет потенциальные риски производственного травматизма.
К примеру, система, установленная на доменной печи №1, покрывает все критически важные участки, включая литейный двор, зону шахты печи, железнодорожный переезд и газоопасные помещения. Видеокамеры с функцией видеоаналитики и специальные персональные устройства обеспечивают круглосуточное наблюдение, определяя местоположение и передвижения работников, а также дистанцию до работающего оборудования. При приближении к опасной зоне сотрудник получает предупредительный звуковой и вибросигнал на своём персональном устройстве, а камеры фиксируют событие для последующего анализа и повышения эффективности мер безопасности.
Очевидно, что будущее металлургии неразрывно связано с дальнейшим внедрением искусственного интеллекта. В ближайшие годы ожидается полная автоматизация литейных и прокатных цехов, где ИИ будет управлять всем производственным циклом — от загрузки сырья до отгрузки готовой продукции.
Егор Петров