В первой части мы рассмотрели, как появились никелевые суперсплавы и как они развивались от 1930-х до начала 80-х годов. В этой части мы рассмотрим дальнейшее развитие суперсплавов на примере лопаток авиационных турбин.
Повышение температуры перед турбиной — один из главных способов увеличить эффективность авиационного двигателя. Чем выше температура, тем больше энергии можно извлечь из топлива, а значит — выше тяга, ниже расход и больше экономичность.
Температура газа в турбине современного боевого истребителя может достигать 1650 °C — это выше температуры плавления большинства конструкционных металлов, таких как медь, никель и даже сталь.
Однако благодаря системе внутреннего охлаждения, теплозащитным керамическим покрытиям и продуманной аэродинамике лопаток температура на их поверхности удерживается на уровне 1100–1150 °C. Тем не менее, и такие условия являются разрушительными для традиционных никелевых суперсплавов (о которых мы писали раньше).
Что касается гражданской авиации, то и здесь температура в зоне лопаток примерно такая же — 1100–1150 °C. Но к этому добавляется ещё одно важное требование: лопатки турбин должны служить 10–20 тысяч часов, тогда как в военной авиации их ресурс обычно ограничивается сотнями, максимум тысячей часов.
И, конечно же, надёжность лопаток напрямую связана с жизнью и безопасностью сотен человек на борту лайнера. Ведь разрушение в полёте даже одной из них может привести к потере управления и катастрофе. Именно здесь, на стыке этих требований, авиационная турбина стала одним из ключевых драйверов эволюции суперсплавов.
На текущем этапе выдерживать такие нагрузки способны только монокристаллы с контролируемой микроструктурой.
Монокристаллы начали применять в 1980-х, и с тех пор технология претерпела серьёзную эволюцию, став основой турбин нового поколения. Это одна из самых технологически сложных областей металлургии, доступная лишь ограниченному кругу стран.
Стоимость говорит сама за себя: в турбинах Boeing 787 на одной ступени работает до 50 монокристаллических лопаток, и каждая, по оценкам, может стоить от 10 000 до 20 000 долларов, то есть до 1 миллиона долларов за комплект. И это только одна ступень из нескольких, работающих в турбине.
Технологиями производства монокристаллических лопаток для авиационных турбин на сегодня владеют: США, Великобритания, Франция, Россия, Китай, Индия Япония и Турция (активно осваивает эту технологию, но пока сильно уступает). Конечно, уровень освоения этих технологий и масштаб их применения в разных странах существенно различаются.
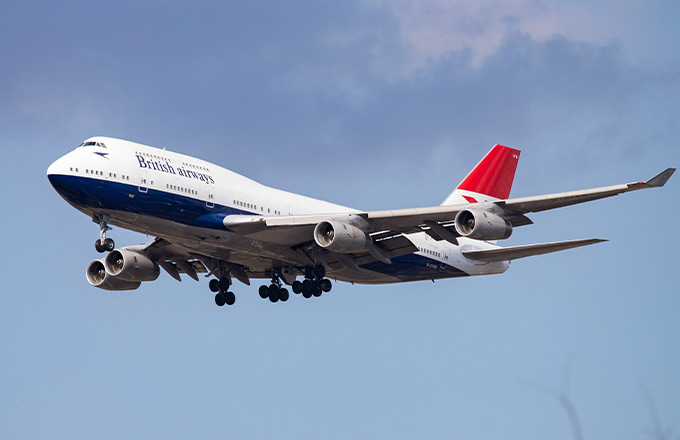
Монокристаллы начали применять в 1980-х, и с тех пор технология претерпела серьёзную эволюцию, став основой турбин нового поколения.
Глобальная технологическая конкуренция
Промышленное лидерство в этой области напрямую связано с обороноспособностью стран, их экономическим суверенитетом и глобальным влиянием. Чтобы удержаться в этой гонке, компании ежегодно вкладывают миллиарды долларов в исследования и разработки.
Мировые лидеры двигателестроения — General Electric, Pratt & Whitney, Rolls-Royce и Safran — не только разрабатывают двигатели, но и напрямую участвуют в создании новых сплавов, от которых зависят ресурс, эффективность и надёжность турбин.
Суперсплавы на пределе
К началу 1980-х дальнейший прогресс в турбинах упёрся в физические пределы: даже никелевые суперсплавы, основной конструкционный материал турбин, начинали терять форму и прочность уже при температуре выше 1000 °C. Это явление известно как ползучесть — медленная пластическая деформация, накапливающаяся под действием высокой температуры и постоянной нагрузки.
Чтобы справиться с новыми вызовами, металлурги двигались в своих поисках в двух направлениях:
- развивали технологию монокристаллов,
- совершенствовали состав и внутреннюю структуру сплавов.
Постепенно это позволило расширить температурный ресурс (то есть предельно допустимую рабочую температуру) материала и повысить надёжность.
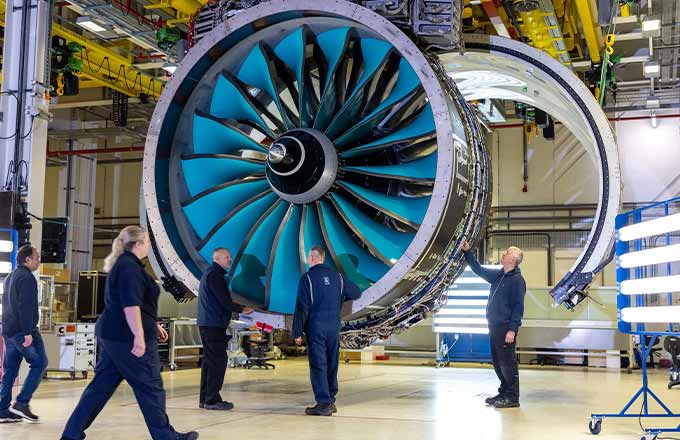
Мировые корпорации ежегодно вкладывают миллиарды долларов в исследования и разработки турбин.
Монокристаллы — прорыв, ставший стандартом
Одним из ключевых прорывов в турбинных технологиях стало литьё лопаток как единого монокристалла.
Если в обычных сплавах металл состоит из множества зёрен, и на границах между ними со временем возникают разрушения, то монокристалл — это материал без таких границ, его кристаллическая решётка непрерывна от основания до вершины детали.
Монокристаллы выращивают прямо в форме, медленно вытягивая металл из зоны затвердевания, чтобы кристалл рос строго в одном направлении. Это придаёт материалу высокую прочность и термостойкость.
Технология зародилась в 1960-х, но стала надёжной лишь к 1980-м и только тогда была внедрена в массовое производство — для наиболее нагруженных деталей турбин.
Впервые монокристаллические лопатки применили в 1970-х — в военных авиадвигателях США, где требовалась максимальная жаростойкость. А с 1980 года технология начала применяться и в гражданской авиации: её внедрили в двигатели для Boeing 747, Airbus A300 и DC-10.
В СССР аналогичные работы стартовали также в 1970-х, но внедрение шло медленнее. Технологию начали осваивать в 1980-х, в том числе в двигателях для истребителей Су-27.
Этот технологический скачок стал по-настоящему переломным: переход от литых и штампованных деталей к монокристаллам позволил существенно повысить рабочие температуры — с прежних 1000–1050 °C до 1100–1150 °C и выше.
Это, в свою очередь, дало резкий прирост КПД турбин и двигателей. А рост эффективности обеспечил колоссальный экономический эффект — от авиации до энергетики.
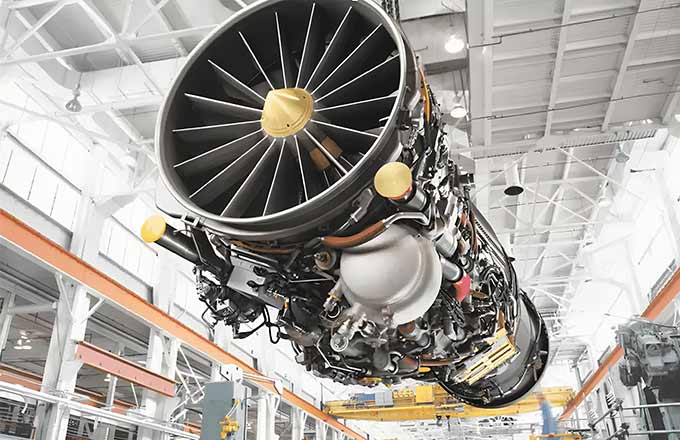
Впервые монокристаллические лопатки применили в 1970-х, с тех пор технологии постоянно совершенствуются.
Микроструктура, которая держит форму
Чтобы металл сохранял форму при высоких температурах, в никелевые сплавы начали добавлять алюминий, титан, тантал и ниобий. Это привело к формированию так называемой γ′-фазы (гамма-штрих) — упрочняющей структуры, равномерно распределённой по всему объёму материала.
γ′-фаза действует как внутренняя арматура — невидимая силовая сетка, пронизывающая металл. Она остаётся стабильной даже при экстремальных температурах, обеспечивая стойкость к ползучести и термической деформации.
В 1980-е годы γ′-структуру стали усиливать добавлением тяжёлых легирующих элементов — прежде всего вольфрама. Это позволило заметно повысить термостойкость и надёжность, особенно в двигателях для Boeing 747, Airbus A300, F-15 и F-16.
В СССР аналогичные технологии начали внедрять ещё в 1970-х — в частности, в двигателях для Су-27 и МиГ-29. Подобные технологии используются и сегодня при производстве современных российских авиадвигателей.
Таким образом, 1980-е стали поворотной точкой: суперсплавы перестали быть просто комбинацией легирующих элементов. Теперь прочность задавалась не только химическим составом, но и внутренней архитектурой материала — на уровне фаз, кристаллической решётки и микроструктурных механизмов.
Так появились материалы нового поколения: уже не просто сложные сплавы, а инженерные системы, выстроенные на уровне кристаллов. Без них невозможно представить современные турбинные двигатели, работающие при температурах выше 1050 °C.
Такие сплавы используются не только в авиации, но и в энергетике — в турбинах ТЭЦ, ГРЭС и АЭС, где металлы годами работают в условиях экстремального нагрева.
Но именно авиация задала самый жёсткий темп: перегрузки, резкие температурные циклы и тысячи градусов потребовали от материалов принципиально нового уровня.
Описанные выше сплавы — с монокристаллической структурой и упрочнением за счёт γ′-фазы — принято считать первым поколением суперсплавов нового типа. Они уже не имели границ зёрен, сохраняли форму при температурах до 1050 °C и стали основой для всего дальнейшего развития никелевых суперсплавов.
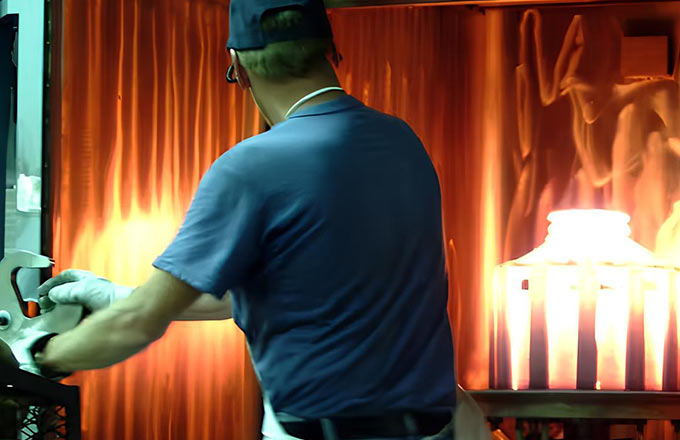
Сплавы с монокристаллической структурой и упрочнением за счёт γ′-фазы принято считать первым поколением суперсплавов нового типа.
Температурный скачок: рений поднял предел, рутений обеспечил стабильность
В 1990–2000-х в состав суперсплавов начали активно добавлять рений (Re) — редкий и тугоплавкий металл, который позволил ещё сильнее замедлить ползучесть и повысить термостойкость при экстремальных нагрузках.
Так появилось второе поколение монокристаллических сплавов: добавка около 3% рения позволила поднять рабочую температуру примерно на 30 °C. В сплавах третьего поколения содержание рения увеличили до 6%, что дало очередной прирост по температурному ресурсу.
Но у рения выявились существенные недостатки. Он не только дорог и дефицитен, но и при высоких концентрациях способствует образованию хрупких фаз, которые со временем разрушают структуру сплава изнутри. Прочность росла, но стабильность падала. Дальнейшее наращивание доли рения оказалось тупиковым — потребовалось новое решение.
Этим решением стал рутений (Ru) — металл платиновой группы, который с начала 2000-х начали добавлять в четвёртом поколении суперсплавов вместе с рением, что помогло сохранить жаростойкость и вернуть стабильность.
Рутений стабилизирует структуру при высоких температурах и препятствует образованию разрушительных фаз.
Это позволило двигателям выйти на новый уровень: рабочая температура достигла 1150 °C, а сплав сохранял форму и прочность в течение десятков тысяч часов.
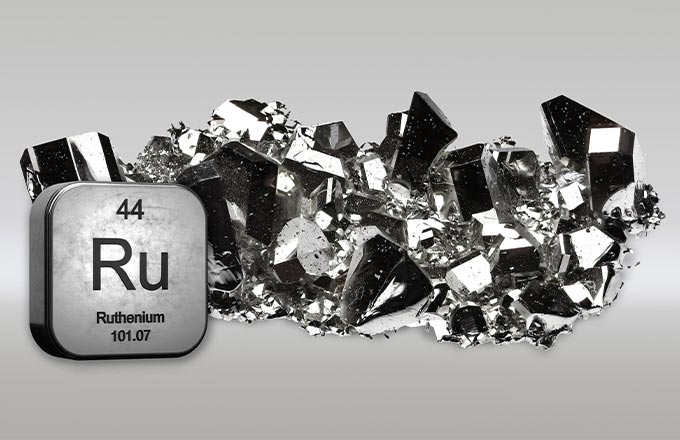
Рутений стабилизирует структуру при высоких температурах и препятствует образованию разрушительных фаз.
Пятое поколение: максимальный баланс
Пятое поколение никелевых суперсплавов стало развитием подхода, заложенного в четвертом: стабилизирующее действие рутения усилили, а соотношение легирующих элементов довели до оптимума. Удалось достичь температуры 1150 °C, при этом выросла стабильность микроструктуры и срок службы лопаток.
Типичные представители поколения 5G — японский TMS-196 и российский ВЖМ8. Эти сплавы применяются в наиболее нагруженных зонах турбин — в военной авиации и энергетике.
Пятое поколение не принесло принципиально новых решений, это скорее результат тонкой настройки, где главное — надёжный баланс между жаростойкостью и структурной стабильностью сплава.
О наличии технологии заявляют несколько стран, но промышленное лидерство по-прежнему принадлежит ограниченному кругу участников.
Разделение суперсплавов на поколения достаточно условно. Ключевое здесь не формальные этапы, а вектор развития: от простого усиления — к управлению структурой — к проектированию материала как системы.
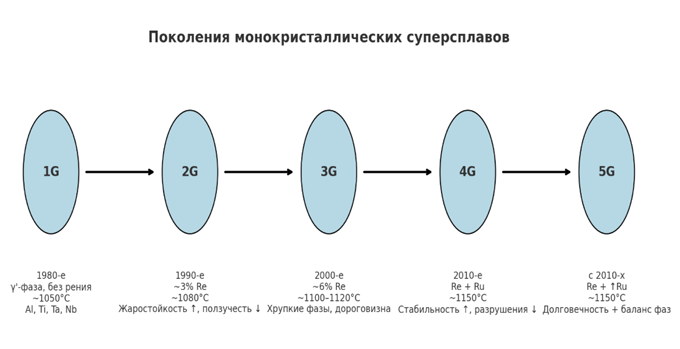
Типичные представители поколения 5G — японский TMS-196 и российский ВЖМ8.
Сплав как инженерная система — следующий шаг
С середины 2010-х начался новый виток развития. Когда подошли к пределу роста жаропрочности за счёт состава, специалисты по материалам переключили своё внимание на архитектуру материала. Одним из таких новых подходов стали градиентные сплавы — в них состав варьируется по объёму детали, что позволяет оптимизировать распределение свойств, улучшая жаропрочность и устойчивость к ползучести
Это дало возможность сократить использование дорогих элементов, таких как рений, сохранив необходимую прочность именно в нагруженных зонах. Цифровое моделирование и управление микроструктурой стали ключевыми инструментами в разработке таких материалов.
Другое перспективное направление — высокоэнтропийные сплавы: материалы на основе нескольких основных элементов в равных пропорциях. Такая структура демонстрирует высокую стабильность и потенциальную жаропрочность.
На первый взгляд это парадокс, ведь со школы мы помним: рост энтропии — синоним распада. Но в случае высокоэнтропийных сплавов всё наоборот — хаотичное распределение атомов создаёт устойчивую однородную фазу.
Такие сплавы считаются перспективными для лопаток турбин и других нагруженных деталей — прежде всего в аэрокосмической отрасли. Исследования в этой области ведутся в ведущих научных центрах от NASA и Rolls-Royce до Института Макса Планка.
Ещё недавно это напоминало научную фантастику. Сегодня — это уже стратегия технологического лидерства.
Но об этом — в третьей части.
Вадим Чепига